Why Plastics Rotomolding is Ideal for Custom-Made Plastic Items
Why Plastics Rotomolding is Ideal for Custom-Made Plastic Items
Blog Article
Pockets rotomolding, or rotational molding, is a production process that's acquired immense popularity for its capacity to create durable, empty elements with exceptional precision. From big professional tanks to small custom components, this approach is known for their versatility and efficiency. Under, we'll discover the key advantages of Parts Plastics Rotomolding and why it's develop into a preferred answer for making high-quality, hollow parts.
What's Pockets Rotomolding?
Rotomolding is a production procedure that involves heat plastic-type inside a revolving mold. This enables the molten plastic to fur the inside surfaces of the mold uniformly, producing useless components with a smooth structure. The end result? Something that is not merely sturdy but also extremely flexible, giving endless applications across industries.

Crucial Advantages of Parts Rotomolding
1. Energy and Longevity
One of many standout benefits of parts rotomolding could be the unmatched longevity it offers. Rotomolded pieces are designed to tolerate severe conditions, including heavy impacts, hard climate, and chemical exposure. This power makes rotomolded areas perfect for programs in industries like automotive, agriculture, and construction.
The seamless, single-piece construction also contributes to the structural reliability of rotomolded products. Unlike other techniques, you can find no stitches or flaws, reducing the risk of breaks or leaks.
2. Cost-Effective Production
Rotomolding is very cost-effective, particularly when making large or complex useless parts. The procedure needs somewhat low tooling fees in comparison to other manufacturing techniques, such as injection molding or blow molding. This makes it especially suited to small-to-medium manufacturing operates without reducing quality.
Also, the capacity to generate components with regular wall depth decreases substance waste, optimizing cost-efficiency even further.
3. Style Freedom
The versatility of rotomolding starts the entranceway to very customizable designs. Whether it's intricate patterns, undercuts, or various wall thicknesses, rotomolding enables suppliers to turn actually the absolute most complicated types in to reality. This flexibility is important for industries that need accuracy and versatility in their components.
More customization options contain textured surfaces, embedded inserts, and also multi-layered areas for included efficiency or strength.
4. Lightweight Yet Robust
Rotomolded pieces achieve the perfect stability between weight and durability. The empty construction decreases material usage, ensuring products and services remain light while maintaining their architectural strength. This really is particularly good for parts such as outdoor gear, tanks, or playground structures, where easy transfer and installation are key considerations.
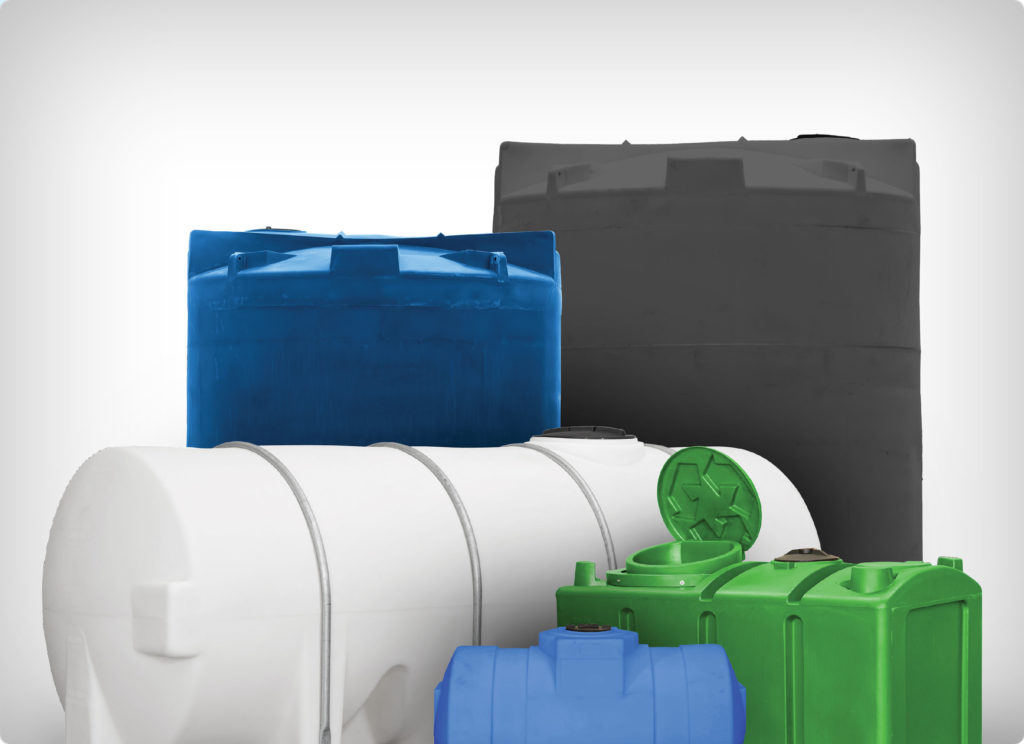
5. Eco-Friendly Production
Rotational molding can be widely celebrated because of its environmental benefits. The procedure effects in small substance waste, as plastic materials can usually be recycled or recycled. Moreover, companies may use eco-friendly components to align with sustainability goals. That jobs rotomolding being an increasingly beautiful selection for agencies seeking to lessen their environmental impact.
Why Parts Rotomolding Stands Out
Pockets rotomolding has revolutionized the manufacturing of durable, empty areas by offering a special mix of strength, cost efficiency, and design flexibility. By leveraging this method, manufacturers may offer supreme quality components that meet the precise needs of varied industries while supporting an eco-conscious approach to production.
If you're buying manufacturing process that delivers smooth longevity and irresistible detail, rotomolding is the answer.
Report this page